Odporne na zużycie (lub odporne na ścieranie) staliwo odnosi się do staliwa o dobrej odporności na zużycie. Według składu chemicznego dzieli się je na staliwo niestopowe, niskostopowe i stopowe odporne na zużycie. Istnieje wiele rodzajów stali trudnościeralnych, które można z grubsza podzielić na: stal wysokomanganową, stal trudnościeralną średnio i niskostopową, stal chromowo-molibdenowo-krzemowo-manganową, stal odporną na kawitację, stal trudnościeralną, i specjalna stal odporna na zużycie. Niektóre stale stopowe, takie jak stal nierdzewna, stal łożyskowa, stopowa stal narzędziowa i stopowa stal konstrukcyjna, są również stosowane jako stal odporna na zużycie w określonych warunkach.
Średnio i niskostopowe stale trudnościeralne zwykle zawierają pierwiastki chemiczne, takie jak krzem, mangan, chrom, molibden, wanad, wolfram, nikiel, tytan, bor, miedź, pierwiastki ziem rzadkich itp. Wykładziny wielu dużych i średnich kulek huty w Stanach Zjednoczonych wykonane są ze stali chromowo-molibdenowo-krzemowo-manganowej lub chromowo-molibdenowej. Większość kul mielących w Stanach Zjednoczonych jest wykonana ze stali chromowo-molibdenowej o średniej i wysokiej zawartości węgla. W przypadku przedmiotów obrabianych, które pracują w stosunkowo wysokiej temperaturze (na przykład 200 ~ 500 ℃) w warunkach zużycia ściernego lub których powierzchnie są poddawane stosunkowo wysokim temperaturom ze względu na ciepło tarcia, stopy takie jak chrom molibdenowo-wanad, chrom molibdenowo-wanadowo-niklowy lub chromowo-molibdenowo-wanadowolframowy można używać.
Ścieranie to zjawisko, w którym materiał na powierzchni roboczej przedmiotu ulega ciągłemu niszczeniu lub utracie w ruchu względnym. Ze względu na mechanizm zużycia zużycie można podzielić na zużycie ścierne, zużycie adhezyjne, zużycie korozyjne, zużycie erozyjne, kontaktowe zużycie zmęczeniowe, zużycie udarowe, zużycie frettingowe i inne kategorie. W przemyśle zużycie ścierne i zużycie adhezyjne stanowią największą część uszkodzeń związanych ze zużyciem przedmiotu obrabianego, a uszkodzenia spowodowane zużyciem, takie jak erozja, korozja, zmęczenie i fretting, zwykle występują podczas pracy niektórych ważnych komponentów, dlatego jest ich coraz więcej. i więcej uwagi. W warunkach pracy często pojawia się kilka form zużycia jednocześnie lub jedna po drugiej, a interakcja uszkodzeń wynikających ze zużycia przybiera bardziej złożoną formę. Określenie rodzaju uszkodzenia ściernego przedmiotu obrabianego jest podstawą rozsądnego wyboru lub opracowania stali trudnościeralnej.
Ponadto zużycie części i komponentów jest problemem inżynierii systemowej. Istnieje wiele czynników wpływających na zużycie, w tym warunki pracy (obciążenie, prędkość, tryb ruchu), warunki smarowania, czynniki środowiskowe (wilgotność, temperatura, otaczające media itp.) i czynniki materiałowe (skład, organizacja, właściwości mechaniczne), powierzchnia jakość oraz właściwości fizyczne i chemiczne części. Zmiany każdego z tych czynników mogą zmienić stopień zużycia, a nawet zmienić mechanizm zużycia. Można zauważyć, że czynnik materiałowy jest tylko jednym z czynników wpływających na zużycie przedmiotu obrabianego. Aby poprawić odporność części stalowych na zużycie, należy zacząć od ogólnego układu tarcia i zużycia w określonych warunkach, aby osiągnąć pożądany efekt.
1. Obróbka cieplna w rozsycie (utwardzanie wodą) odpornych na zużycie odlewów ze stali wysokomanganowej
W strukturze po odlaniu odpornej na zużycie stali wysokomanganowej występuje duża liczba wydzielonych węglików. Węgliki te zmniejszają wytrzymałość odlewu i ułatwiają pękanie podczas użytkowania. Głównym celem obróbki cieplnej odlewów ze stali wysokomanganowych jest eliminacja węglików w strukturze w stanie surowym oraz na granicach ziaren w celu uzyskania jednofazowej struktury austenitu. Może to poprawić wytrzymałość i wytrzymałość stali wysokomanganowej, dzięki czemu odlewy ze stali wysokomanganowej nadają się do szerszego zakresu dziedzin.
Obróbkę cieplną przesycającą odpornych na zużycie odlewów ze stali wysokomanganowych można z grubsza podzielić na kilka etapów: nagrzanie odlewów do temperatury powyżej 1040°C i przetrzymanie ich przez odpowiedni czas, tak aby zawarte w nich węgliki całkowicie rozpuściły się w austenicie jednofazowym ; następnie szybko schładzając, uzyskaj strukturę stałego roztworu austenitu. Ta obróbka roztworowa nazywana jest również obróbką hartowania wodą.
(1) Temperatura hartowania w wodzie
Temperatura twardości wody zależy od składu chemicznego stali wysokomanganowej, zwykle 1050 ℃ -1100 ℃. Stale wysokomanganowe o dużej zawartości węgla lub o dużej zawartości stopów (takie jak stal ZG120Mn13Cr2 i stal ZG120Mn17) powinny przyjmować górną granicę temperatury udarności w wodzie. Jednakże zbyt wysoka temperatura twardości wody spowoduje silne odwęglenie powierzchni odlewu i szybki wzrost ziaren stali wysokomanganowej, co będzie miało wpływ na parametry użytkowe stali wysokomanganowej.
(2) Szybkość ogrzewania podczas hartowania w wodzie
Przewodność cieplna stali manganowej jest gorsza niż zwykłej stali węglowej. Odlewy ze stali wysokomanganowej charakteryzują się dużymi naprężeniami i łatwo pękają pod wpływem ogrzewania, dlatego szybkość nagrzewania należy ustalać w zależności od grubości ścianki i kształtu odlewu. Ogólnie rzecz biorąc, odlewy o mniejszej grubości ścianki i prostej konstrukcji można nagrzewać szybciej; odlewy o większej grubości ścianek i złożonej budowie należy nagrzewać powoli. W rzeczywistym procesie obróbki cieplnej, aby zmniejszyć odkształcenie lub pękanie odlewu podczas procesu nagrzewania, na ogół podgrzewa się go do około 650 ℃, aby utrzymać zmniejszoną różnicę temperatur pomiędzy wnętrzem i zewnętrzem odlewu, a temperaturę w piec jest jednolity, a następnie szybko osiąga temperaturę twardości wody.
(3) Czas utrzymywania procesu hartowania w wodzie
Czas utrzymywania procesu hartowania w wodzie zależy głównie od grubości ścianki odlewu, aby zapewnić całkowite rozpuszczenie węglików w strukturze odlanej i homogenizację struktury austenitu. W normalnych warunkach można go obliczyć, zwiększając czas wytrzymywania o 1 godzinę na każde 25 mm wzrostu grubości ścianki.
(4) Chłodzenie procesu hartowania w wodzie
Proces chłodzenia ma duży wpływ na wskaźnik wydajności i strukturę odlewu. Podczas hartowania w wodzie temperatura odlewu przed wejściem do wody powinna przekraczać 950°C, aby zapobiec ponownemu wytrącaniu się węglików. Z tego powodu odstęp czasu pomiędzy wylaniem z pieca a wejściem do wody nie powinien przekraczać 30 sekund. Temperatura wody powinna być niższa niż 30°C przed wejściem odlewu do wody, a maksymalna temperatura wody po wejściu do wody nie powinna przekraczać 50°C.
(5) Węglik po hartowaniu w wodzie
Jeśli po hartowaniu w wodzie całkowicie wyeliminowane zostaną węgliki ze stali wysokomanganowej, uzyskana w tym czasie struktura metalograficzna będzie strukturą jednoaustenityczną. Ale taką strukturę można uzyskać tylko w odlewach cienkościennych. Generalnie dopuszcza się niewielką ilość węglików w ziarnach austenitu lub na granicach ziaren. Nierozpuszczone węgliki i wytrącone węgliki można ponownie wyeliminować poprzez obróbkę cieplną. Jednakże węgliki eutektyczne wytrącające się w wyniku nadmiernej temperatury ogrzewania podczas hartowania w wodzie są niedopuszczalne. Ponieważ węglika eutektycznego nie można ponownie wyeliminować poprzez obróbkę cieplną.
2. Obróbka cieplna wzmacniająca wytrącanie odpornych na zużycie odlewów ze stali wysokohanganowej
Obróbka cieplna wzmacniająca wytrącanie odpornej na zużycie stali wysokomanganowej oznacza dodanie pewnej ilości pierwiastków tworzących węgliki (takich jak molibden, wolfram, wanad, tytan, niob i chrom) poprzez obróbkę cieplną w celu uzyskania określonej ilości i rozmiaru w stal wysokomanganowa Druga faza rozproszonych cząstek węglika. Ta obróbka cieplna może wzmocnić osnowę austenityczną i poprawić odporność na zużycie stali wysokomanganowej.
3. Obróbka cieplna odpornych na zużycie odlewów ze stali średniochromowej
Celem obróbki cieplnej odpornych na zużycie odlewów ze stali średniochromowej jest uzyskanie struktury osnowy martenzytycznej o dużej wytrzymałości, ciągliwości i dużej twardości, tak aby poprawić wytrzymałość, ciągliwość i odporność na zużycie odlewów stalowych.
Odporna na zużycie stal średniochromowa zawiera więcej pierwiastków chromowych i ma wyższą hartowność. Dlatego jego zwykłą metodą obróbki cieplnej jest: po 950 ℃ - 1000 ℃, austenityzacja, następnie hartowanie i terminowa obróbka odpuszczająca (zwykle w temperaturze 200-300 ℃).
4. Obróbka cieplna odpornych na zużycie odlewów ze stali niskostopowych
Odporne na zużycie odlewy ze stali niskostopowych poddawane są obróbce poprzez hartowanie w wodzie, hartowanie w oleju i hartowanie w powietrzu w zależności od składu stopu i zawartości węgla. Staliwo perlityczne odporne na zużycie przyjmuje obróbkę cieplną normalizującą i odpuszczającą.
W celu uzyskania osnowy martenzytycznej o dużej wytrzymałości, ciągliwości i twardości oraz polepszenia odporności odlewów stalowych na zużycie, odporne na zużycie odlewy ze stali niskostopowych poddaje się zazwyczaj hartowaniu w temperaturze 850-950°C i odpuszczaniu w temperaturze 200-300°C .
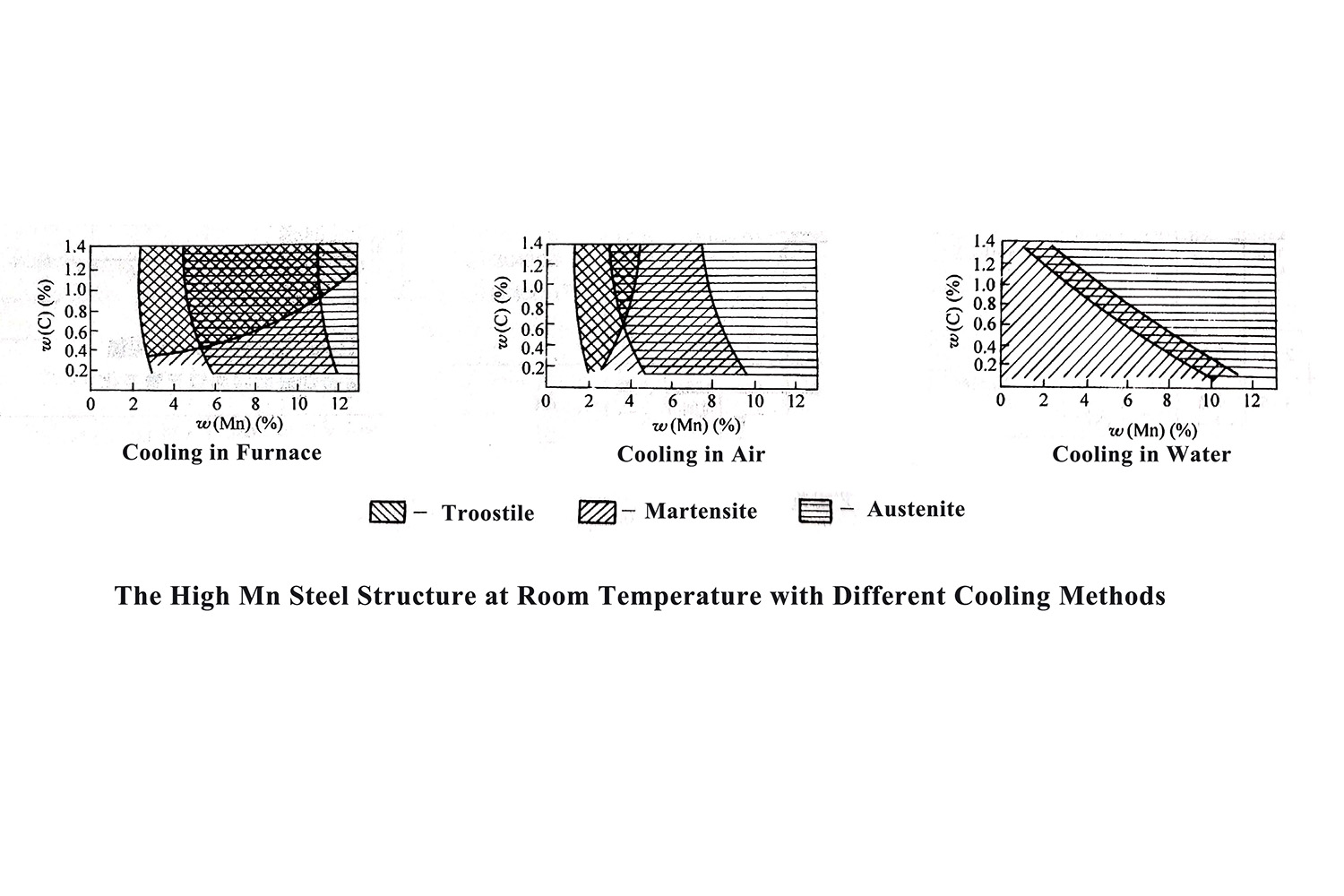
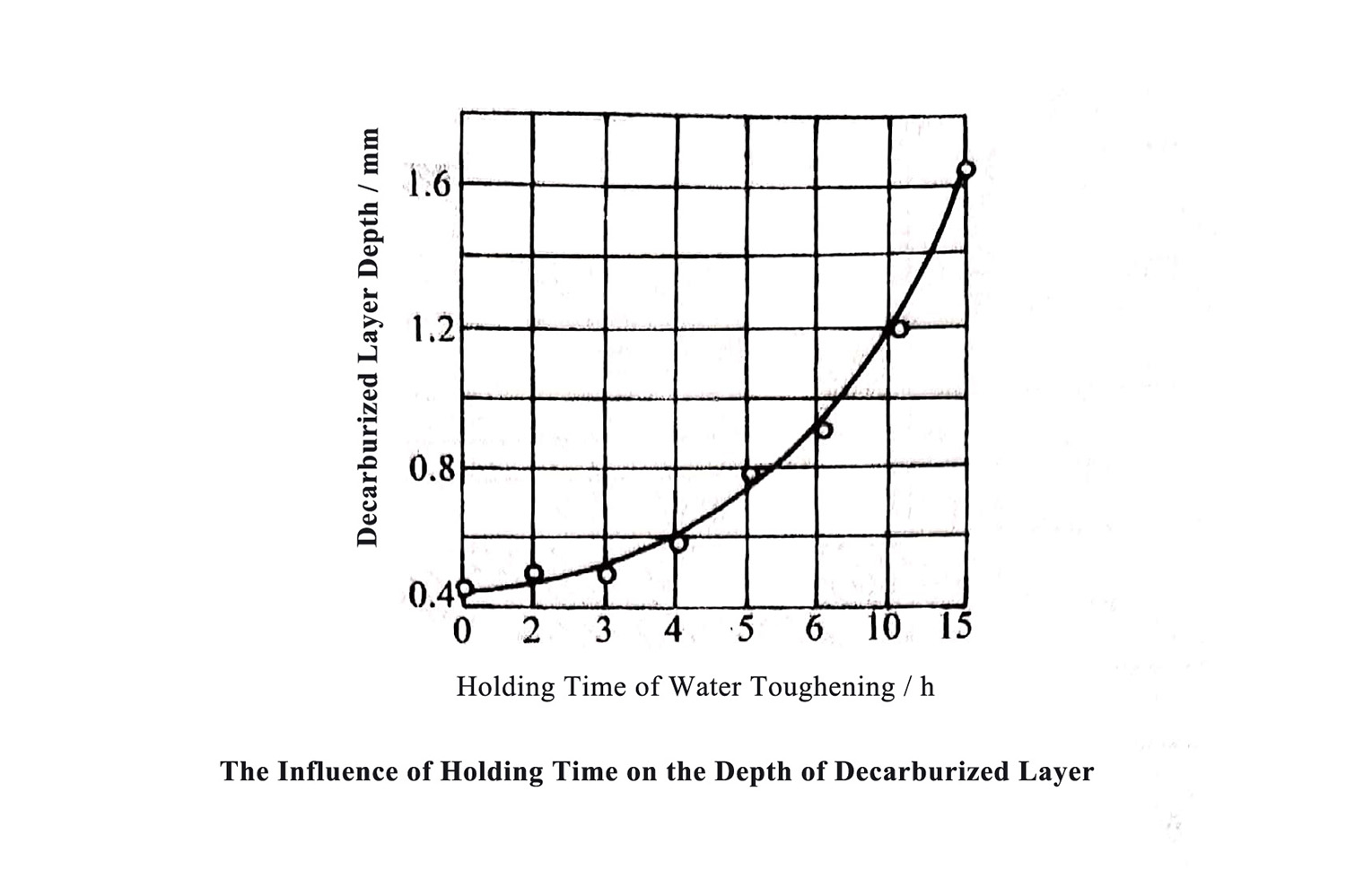
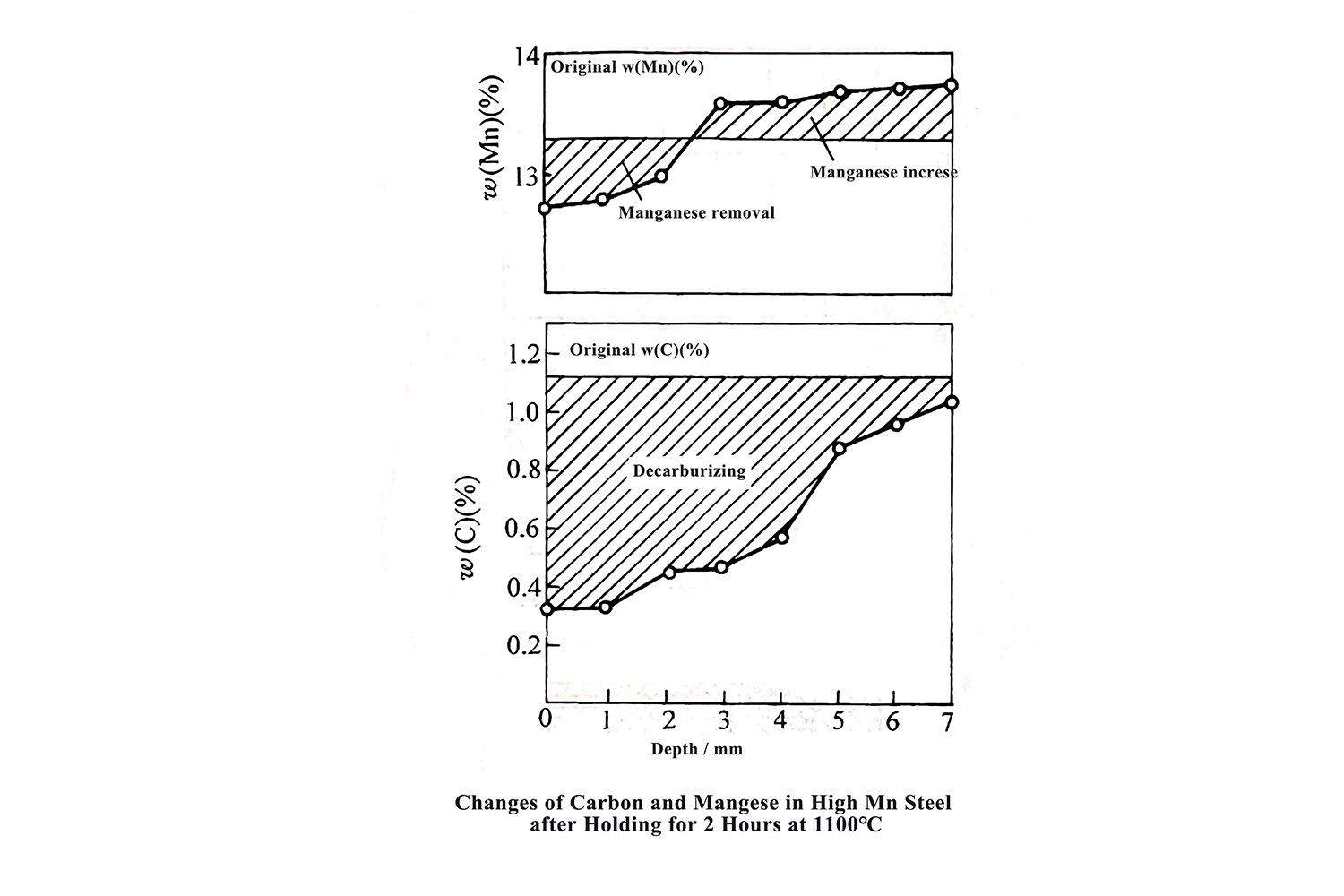
Czas publikacji: 07 sierpnia 2021 r