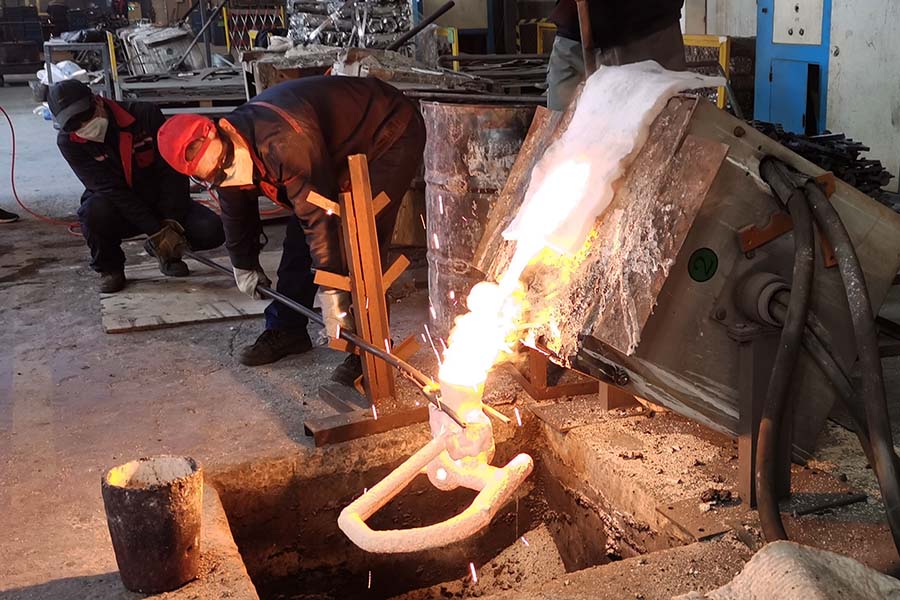
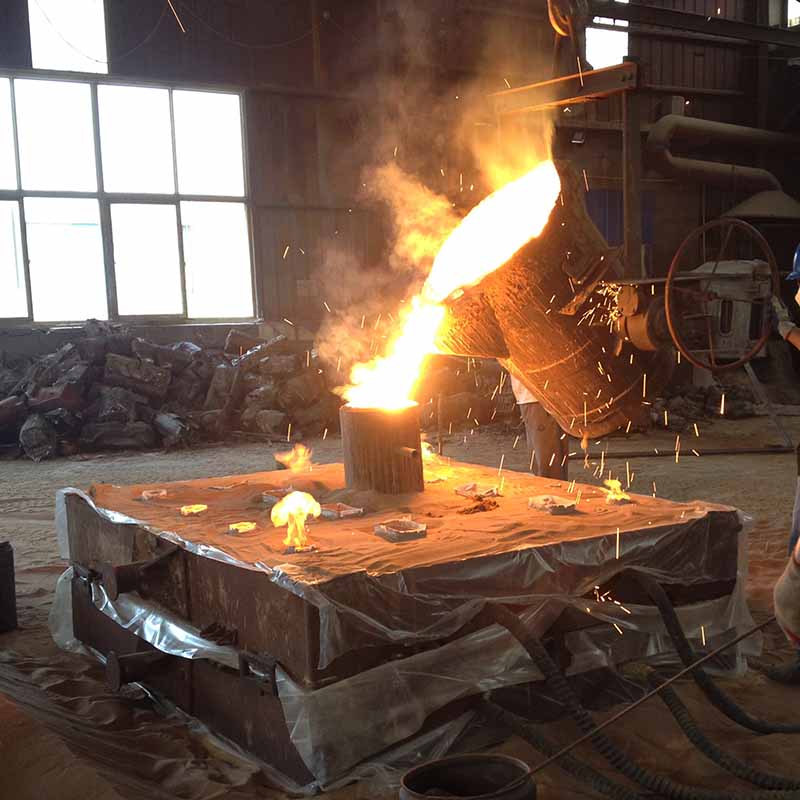
Odlewanie jest jedną z najwcześniejszych znanych ludzkości metod kształtowania metali. Ogólnie oznacza to wlewanie stopionego metalu do ogniotrwałej formy z wnęką o kształcie, który ma zostać wykonany, i pozostawienie jej do zestalenia. Gdyzestalony, pożądany przedmiot metalowy wyjmuje się z formy ogniotrwałej albo przez rozbicie formy, albo przez rozebranie formy. Zestalony obiekt nazywa się odlewaniem. Proces ten nazywany jest także odlewaniem, a nowoczesną fabryką zajmującą się odlewaniem części metalowychodlewnia.
1. Historia procesu odlewniczego
Proces odlewania odkryto prawdopodobnie około 3500 roku p.n.e. w Mezopotamii. W tym okresie w wielu częściach świata miedziane topory i inne płaskie przedmioty formowano w otwartych formach z kamienia lub wypalanychglina. Formy te były zasadniczo jednoczęściowe. Jednak w późniejszych okresach, gdy zaczęto wytwarzać okrągłe przedmioty, formy takie dzielono na dwie lub więcej części, aby ułatwić wyjmowanie okrągłych przedmiotówEpoka brązu (ok. 2000 r. p.n.e.) przyniosła znacznie większe udoskonalenie procesu odlewania. Być może po raz pierwszy wynaleziono rdzeń do wykonywania pustych kieszeni w przedmiotach. Rdzenie te wykonano z wypalanej gliny.Ponadto proces cire perdue, czyli wosku traconego, był szeroko stosowany do wyrobu ozdób i drobnych prac.
Technologia odlewania została znacznie udoskonalona przez Chińczyków od około 1500 roku p.n.e. Wcześniej nie ma dowodów na jakąkolwiek działalność castingową w Chinach. Nie wydają się być wspaniałenie znał procesu cire perdue, ani nie stosował go szeroko, ale zamiast tego specjalizował się w wieloczęściowych formach do wykonywania bardzo skomplikowanych prac. Spędzili dużo czasu na dopracowaniu formy w najdrobniejszych szczegółach, więc trudnoPrzy odlewie wykonanym z form wymagane były wszelkie prace wykończeniowe. Prawdopodobnie wykonali formy kawałkowe zawierające starannie dopasowane elementy w liczbie trzydziestu lub więcej. W rzeczywistości odkryto wiele takich pleśnipodczas wykopalisk archeologicznych w różnych częściach Chin.
Cywilizacja doliny Indusu znana jest również z szerokiego stosowania odlewów z miedzi i brązu do ozdób, broni, narzędzi i przyborów kuchennych. Jednak w technologii nie nastąpił duży postęp. Z variJeśli chodzi o przedmioty i figurki wydobyte w dolinie Indusu, wydaje się, że znali wszystkie znane metody odlewania, takie jak forma otwarta, forma kawałkowa i proces cire perdue.
Chociaż Indiom można przypisać wynalezienie stali tyglowej, niewiele z odlewnictwa żelaza było w Indiach widocznych. Istnieją dowody na to, że odlewanie żelaza rozpoczęło się około 1000 roku p.n.e. w Syrii i Persji. Wydaje sięToodlewanie żelazatechnologia w Indiach była stosowana od czasów najazdu Aleksandra Wielkiego, około 300 roku p.n.e.
Słynny żelazny filar znajdujący się obecnie w pobliżu minaru Qutb w Delhi jest przykładem metalurgicznych umiejętności starożytnych Indian. Ma 7,2 m długości i jest wykonany z czystego żeliwa ciągliwego. Zakłada się, że jest to zokres Chandragupty II (375-413 n.e.) z dynastii Guptów. Stopień rdzewienia tego słupa, który stoi na zewnątrz, na świeżym powietrzu, jest praktycznie zerowy i nawet zakopana część rdzewieje w niezwykle powolnym tempie. Tenmusiał zostać najpierw odlany, a następnie młotkowany do ostatecznego kształtu.
2. Zalety i ograniczenia
Proces odlewania jest szeroko stosowany w produkcji ze względu na wiele zalet. Stopiony materiał przepływa do dowolnej małej sekcji we wnęce formy i jako taki ma dowolny skomplikowany kształt – wewnątrzlub zewnętrzne – mogą być wykonane metodą odlewania. Możliwe jest odlewanie praktycznie każdego materiału, zarówno żelaznego, jak i nieżelaznego. Ponadto niezbędne narzędzia wymagane do form odlewniczych są bardzo proste iniedrogi. Dzięki temu przy produkcji próbnej lub produkcji małej partii jest to metoda idealna. W procesie odlewania możliwe jest umieszczenie takiej ilości materiału, jaka jest dokładnie potrzebna. W rezultaciemożna osiągnąć redukcję masy w projekcie.Odlewysą na ogół chłodzone równomiernie ze wszystkich stron i dlatego oczekuje się, że nie będą miały właściwości kierunkowych. Istnieją pewne metale i stopyktóre można przetwarzać wyłącznie poprzez odlewanie, a nie w żadnym innym procesie, takim jak kucie, ze względów metalurgicznych. Istnieje możliwość wykonania odlewów o dowolnej wielkości i wadze, nawet do 200 ton.
Jednak dokładność wymiarowa i wykończenie powierzchni osiągane są normalnieproces odlewania piaskuw wielu przypadkach nie byłyby odpowiednie do ostatecznego zastosowania. Aby uwzględnić te przypadki, przeprowadzono specjalny castingopracowano procesy takie jak odlewanie ciśnieniowe, których szczegóły podano w późniejszych rozdziałach. Również proces odlewania w piasku jest w pewnym stopniu pracochłonny i dlatego też zmierza się w jego kierunku wiele udoskonaleń,takie jak formowanie maszynowe i mechanizacja odlewni. W przypadku niektórych materiałów często trudno jest usunąć defekty powstałe na skutek obecności wilgociodlewy piaskowe.
3. Warunki castingu
W kolejnych rozdziałach zostaną przedstawione szczegóły odlewania w piasku, które przedstawiają podstawowy proces odlewania. Zanim przejdziemy do szczegółów procesu, zdefiniujmy liczbę słów słownictwa rzucanegoodpowiedni.
Kolba– Kolba formierska to taka, która utrzymuje formę piaskową w nienaruszonym stanie. W zależności od położenia kolby w strukturze formy, określa się ją różnymi nazwami, takimi jak przeciąganie, kopytko i policzek. Wykonany jest z drewnado zastosowań tymczasowych lub bardziej ogólnie z metalu do użytku długotrwałego.
Ciągnąć– Dolna skrzynka formierska
Radzić sobie– Górna skrzynka formierska
Policzek– Pośrednia skrzynka formierska stosowana przy formowaniu trójczęściowym.
Wzór– Wzór jest repliką finalnego obiektu, który należy wykonać z pewnymi modyfikacjami. Wnęka formy jest wykonywana za pomocą wzoru.
Linia podziału– Jest to linia podziału pomiędzy dwiema skrzynkami formierskimi tworzącymi formę piaskową. W przypadku wzoru podziału jest to również linia podziału pomiędzy dwiema połówkami wzoru
Płyta dolna– Jest to deska zwykle wykonana z drewna, używana na początku wykonywania form. Wzór utrzymuje się najpierw na desce dolnej, posypuje się go piaskiem, a następnie wykonuje się ubijanie w ciągu.
W obliczu piasku– Niewielka ilość materiału węglowego nasypana na wewnętrzną powierzchnię wnęki formierskiej w celu zapewnienia lepszego wykończenia powierzchni odlewów
Piasek formierski– Jest to świeżo przygotowany materiał ogniotrwały używany do wykonania wnęki formy. Jest to mieszanina glinki krzemionkowej i wilgoci w odpowiednich proporcjach, aby uzyskać pożądane efekty i otaczawzór podczas wykonywania formy.
Piasek podkładowy– Stanowi większość materiału ogniotrwałego znajdującego się w formie. Składa się ze zużytego i spalonego piasku.
Rdzeń– Służy do wykonywania pustek w odlewach.
Basen do nalewania– Mała wnęka w kształcie lejka na górze formy, do której wlewa się roztopiony metal.
Szaleństwo– Kanał, przez który stopiony metal z wanny odlewniczej dociera do gniazda formy. W wielu przypadkach kontroluje przepływ metalu do formy.
Biegacz– Kanały w płaszczyźnie podziału, przez które regulowany jest przepływ stopionego metalu, zanim dotrze on do gniazda formy.
Brama– Rzeczywisty punkt wejścia, przez który stopiony metal dostaje się do gniazda formy.
Wianuszek– Koronki służą do podparcia rdzeni wewnątrz gniazda formy, aby zadbać o swój własny ciężar i pokonać siły metalostatyczne.
Chłod– Dreszcze to metalowe przedmioty, które umieszcza się w formie w celu zwiększenia szybkości chłodzenia odlewów i zapewnienia równomiernej lub pożądanej szybkości chłodzenia.
Pion– Jest to zbiornik roztopionego metalu znajdujący się w odlewie, dzięki czemu gorący metal może spłynąć z powrotem do gniazda formy, gdy nastąpi zmniejszenie objętości metalu w wyniku krzepnięcia
4. Procedura wykonywania form piaskowych
Procedura wykonywania typowej formy piaskowej jest opisana w następujących krokach:
W pierwszej kolejności na platformę formierską lub na podłogę kładzie się deskę dolną, wyrównując powierzchnię. Skrzynka formierska ciągniona jest trzymana do góry nogami na płycie dolnej wraz z częścią przeciąganąwzór na środku kolby na desce. Pomiędzy wzorem a ściankami kolby powinien być wystarczający odstęp, rzędu 50 do 100 mm. Posypuje się suchy piasek licowydeskę i wzór, aby zapewnić nieklejącą się warstwę. Świeżo przygotowany piasek formierski odpowiedniej jakości wsypuje się teraz do włókien i modelu na grubość od 30 do 50 mm. Reszta kolby przeciąganej jestcałkowicie wypełniony piaskiem zapasowym i równomiernie ubijany w celu zagęszczenia piasku. Ubijanie piasku należy wykonywać prawidłowo, tak aby nie doszło do jego zbyt silnego ubicia, co utrudnia ulatnianie się gazów,ani zbyt luźne, aby forma nie miała wystarczającej wytrzymałości. Po zakończeniu ubijania nadmiar piasku w kolbie całkowicie zeskrobujemy za pomocą płaskownika do poziomu krawędzi kolby.
Teraz za pomocą drutu odpowietrzającego, czyli drutu o średnicy od 1 do 2 mm zakończonego zaostrzonym zakończeniem, w przeciągarce wykonuje się otwory odpowietrzające na całą głębokość kolby oraz na wzór ułatwiający usuwanie gazów podczas castinguzestalenie. To kończy przygotowanie przeciągania.
Gotową kolbę przeciąganą przetacza się teraz na dolną deskę, odsłaniając wzór pokazany na zdjęciu. Za pomocą gładzi naprawia się krawędzie piasku wokół wzoru i nakłada na niego połowę wzoruwzór przeciągania, wyrównując go za pomocą kołków ustalających. Kolba górna na górze hamulca jest ponownie ustawiana w jednej linii za pomocą kołków. Cały drag i wzór posypujemy suchym piaskiem rozdzielającym.
Kołek wlewowy służący do wykonania przejścia wlewowego znajduje się w niewielkiej odległości około 50 mm od szablonu. W odpowiednim miejscu trzyma się także kołek nadstawki, jeśli jest to wymagane, oraz świeżo przygotowaną masę formierską podobną do tegoposypuje się włókę wraz z piaskiem podkładowym. Piasek jest dokładnie ubijany, nadmiar piasku zeskrobany, a w całym kopycie, podobnie jak w oporze, wykonane są otwory wentylacyjne.
Trzpień wlewowy i kołek pionowy są ostrożnie wyjmowane z kolby. Później w pobliżu szczytu wlewu wycina się misę wylewową. Kapa jest oddzielona od hamulca i luźnego piasku na styku kapy i hamulcaoporu jest wydmuchiwany za pomocą miechów. Teraz połówki kapy i wzoru oporu są wycofywane za pomocą kolców ściągających i uderzania wzoru dookoła, aby nieznacznie powiększyć wnękę formy, tak abyŚciany formy nie są niszczone przez wzór wycofywania. Prowadnice i bramki są wycinane w formie ostrożnie, nie niszcząc formy. Nadmiar lub luźny piasek znajdujący się w kanałach i zagłębieniu formy jest wydmuchiwanyza pomocą miechów. Teraz na całą wnękę formy i wlewy nakłada się piasek licowy w postaci pasty, co zapewni dobre wykończenie powierzchni gotowego odlewu.
Rdzeń z suchego piasku przygotowuje się za pomocą rdzennicy. Po odpowiednim wypieczeniu umieszcza się go w gnieździe formy jak pokazano na zdjęciu. Kapa jest umieszczana na hamulcu, dbając o wyrównanie obu za pomocąszpilki. Na kapie utrzymuje się odpowiedni ciężar, aby zadbać o siłę metalostatyczną skierowaną ku górze podczas zalewania stopionego metalu. Forma, jak pokazano na zdjęciu, jest teraz gotowa do zalewania.
Czas publikacji: 25 grudnia 2020 r